Дробилка зерна в приготовлении комбикорма
Процесс дробления зерна
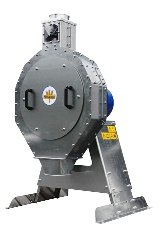
Один из самых важных этапов в процессе приготовления высококачественного комбикорма это измельчение (дробление) исходных компонентов.
Дробление – это достаточно энергоемкая технологическая операция, которая выполняется в процессе подготовки исходных компонентов к смешиванию. Измельчению подлежат зерновые (кукуруза, пшеница, ячмень и др.), шроты (соевый, подсолнечниковый и др.), сырье минерального происхождения, другие компоненты.
При производстве премиксов измельчают наполняющую часть – как правило это отруби, соли микроэлементов. При производстве комбикормов для ценных пород рыбы нужно измельчать практически все компоненты комбикорма до высокого уровня дисперсности, особенно это относится к стартовым комбикормам.
Измельчать необходимо сырье, поступающее как в гранулированном виде, так и гранулы комбикорма при производстве крупки или крошки.
В ряде случаев на комбикормовых предприятиях производят пропаренные и плющеные хлопья. Для их изготовления применяют вальцовые плющилки для получения плющенного зерна.
Степень измельчения зерна дробилкой
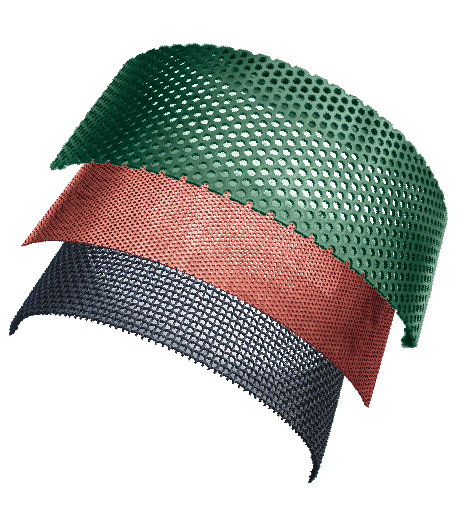
Важными показателями качества измельчения компонентов комбикорма является степень измельчения. Контролируется степень измельчения по результатам изучения остатков на ситах специальных приборов-классификаторов. Диаметр отверстий в ситах таких приборов 5, 3 и 2 мм. Качество помола определяют по ГОСТ 13496.8-92.
Остаток на сите с диаметром отверстий 2 мм при мелком помоле (размеры частиц 0,2... 1 мм) не должен превышать 5 %; при среднем уровне помола (1... 1,8 мм) остаток на сите с отверстиями диаметром 3 мм должен быть не более 12 %; при крупном помоле (1,8...2,6 мм) остаток на сите с отверстиями диаметром 3 мм' должен быть не более 35 % и на сите с отверстиями диаметром 5 мм - не более 5 %.
Уровень измельчения зерна определяется исходя из рецепта комбикорма. Нужная степень измельчения достигается путем подбора решет для дробилки с соответствующим диаметром отверстий. Большинство производителей дробилок зерна предлагают сита с диаметром отверстий начиная с 2мм. Для дековых или дисковых дробилок степень помола регулируется расстоянием между дисками или регулировкой зазора между молотками и декой.
Уровень измельчения зерновых, а также способ этого измельчения (плющение или дробление) существенно влияет на уровень усвояемости питательных веществ животными и на их привесы. Требуемая степень измельчения зерна уровнем влажности до 14 % достигается комплектацией дробилок решетами с отверстиями диаметром: при мелком помоле – 2-3 мм, среднем – 3,5-5, крупном - 6-8 мм.
Этап смешивания измельченных компонентов
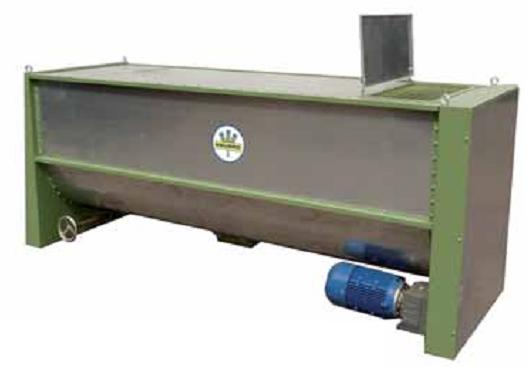
Благодаря смешиванию компонентов комбикорма достигается равномерное распределение частиц компонентов комбикорма в общем его объеме. Результатом смешивания является гомогенный однородный комбикорм. В технологических линиях комбикормовых предприятий применяется процесс механического смешивания. Исходя из агрегатного состояния смешиваемых веществ в производстве применяют различные виды смесителей. Смесители могут быть горизонтальными, вертикальными или диагональными. Существуют также смесители для приготовления жидкого корма – исходные компоненты комбикорма подаются в смеситель, к ним добавляется вода и в процессе перемешивания достигается однородная масса.
Эффективность смешивания комбикорма определяется степенью однородности получаемой комбикормовой смеси. В идеальной смеси содержание составляющих комепонентов в долях или процентах должно быть одинаковым в любой единице объема, начиная от объема всей смеси и заканчивая самым маленьким объемом, зависящим от размера частиц смешиваемых ингредиентов.
Практически невозможно получить абсолютно однородную смесь различных сыпучих компонентов, поскольку при любом процессе смешивания одновременно идет и процесс разделения смеси.
Процесс измельчения исходных компонентов в технологии производства комбикорма необходимо налаживать исходя от перерабатываемого сырья и того, каким животным предназначается комбикорм, а также в каком виде он будет скармливаться - в рассыпном или гранулированном. Для равномерности распределения частиц с маленькой или очень маленькой долей содержания в массе комбикорма решающее значение имеет его дисперсность. Считают, чем меньше доля компонента в рецептуре, тем тоньше он должен быть измельчен для получения примерно такого же суммарного количества частиц, как у компонентов с крупной и средней долей.
Качество смешивания комбикорма определяется многими факторами.
Движение частиц в смесителях и процесс смешивания зависит от таких факторов:
- способа загрузки материала в смеситель;
- скорости вращения рабочих органов смесителя;
- формы смесителя и его рабочих органов;
- качества и объемов дозирования компонентов;
- соотношения между компонентами;
- уровня загрузки смесителя;
- соотношения удельного и насыпного веса компонентов смеси;
- величина коэффициентов внешнего трения между частицами;
- форма и размер частиц;
- степень измельчения отдельных ингредиентов;
- влажность смеси и отдельных компонентов;
- вида основного наполнителя.
Процесс измельчения исходных компонентов комбикорма строят по двум возможным вариантам:
1. Последовательное измельчение исходных компонентов до направления их на взвешивание и подачу в смеситель; при наличии нескольких линий измельчения компоненты распределяют по линиям, а в каждой линии последовательный принцип сохраняют;
2. Измельчение смесей компонентов после их дозирования. Здесь возможно несколько решений.
Cледующий этап приготовления комбикорма это смешивание компонентов. Смешивание - механический процесс. В процессе смешивания компоненты комбикорма не меняют химических свойств, осуществляется только механическое равномерное распределение частиц в общей массе.
В зависимости от особенностей протекания технологического процесса смесители можно разделить на такие группы:
- 1) смесители периодического действия;
- 2) смесители непрерывного действия;
Для дробления исходных компонентов в комбикормовых цехах и на предприятиях производящих премиксы применяются молотковые дробилки зерна, плющилки, дезинтеграторы (дисмембраторы), дисковые, ножевые, шрифтовые, зубчатые, а также валковые измельчители гранул, и др.
Наиболее распространены в промышленности по производству кормов молотковые дробилки. Благодаря простоте конструкции и легкости обслуживания таким дробилкам отдает преимущество большинство производителей комбикорма. Такие дробилки могут отличаться конструкцией.
Молотковые дробилки зерна - это измельчители ударного. Кроме простота устройства они также характеризуются высокой надежностью в работе, компактностью, гибкостью в настройках, невысокой стоимостью.
Для производства комбикормов используют дробилки закрытого типа. В дробилках закрытого типа сита закрывают всю барабанную камеру. Продукт, который попадает в дробильную камеру, в процессе перемещения совершает многократные круговые движения, распределяясь по камере в виде рыхлой субстанции. В дробильной камере продукт измельчается благодаря многократному действию ударной силы молотков при столкновении с частицами продукта в движущемся слое измельчаемого материала.
Вместе с преимуществами молотковые дробилки имеют и ряд недостатков:
- относительно высокая энергоемкость,
- неравномерность гранулометрического состава получаемого продукта с повышенным содержанием сильно измельченных частиц,
- сильный износ рабочих органов.
Для дозирования компонентов комбикорма можно использовать как объемные, так и весовые дозаторы. Объемные дозаторы представлены барабанными, шнековыми, тарельчатыми, вибрационными, аэрационными, комбинированные и другие устройства, предназначенные для отмеривания объемов сыпучего материала. Объемное дозирование – процесс непрерывный.
Все компоненты дозируются одновременно. Объемные дозаторы обеспечивают в обычных условиях работы сравнительно низкую точность дозирования (+3 %) с большими отклонениями от среднего. Весовое дозирование является наиболее точным. С помощью весов определяется точный вес каждого компонента комбикорма. Готовый комбикорм получается более качественным, соотношение компонентов в комбикорме полностью соответствует рецептуре.
Выбор смесителя периодического действия сводится к определению емкости смесителя исходя из производительности технологической линии и операционного времени, а также от состава смеси для производства комбикормов.
На рынке представлено много различных видов смесителей комбикорма. Они различаются по конструкции, принципу смешивания и другим параметрам. В зависимости от вида смешиваемых кормов смесители могут быть предназначены для приготовления сухих сыпучих (комбикормов), рассыпных влажных и жидких (консистентных) кормов.
Виды смесителей комбикорма
Можно выделить такие типы смесителей: барабанные, горизонтальные, вертикальные или диагональные смесители разные по конструкции, а таке смесители с мешалками. Смесители различают также по конструкции рабочих органов: шнековые, лопастные и ленточные. Для жидких - турбинные, пропеллерные и лопастные, а для рассыпных влажных (стебельных) кормов - шнековые и лопастные.
Горизонтальный, диагональный и вертикальный смесители комбикорма:
![]() |
![]() |
![]() |
Смесители отличаются и по частоте вращения мешалок – есть тихоходные и быстроходные.
Горизонтальные смесители применяют для смешивания всех видов сухих и влажных компонентов, за исключением жидких кормосмесей. В процессе работы компоненты комбикорма загружают в бункер смесителя, интенсивно перемешиваются вращающимся внутри корытообразного цилиндрического корпуса шнеком или валом с лопастями, которые расположены по винтовой линии. При этом слои корма, перемешиваясь один относительно другого с различными окружными скоростями, проталкиваются к разгрузочному окну.
Применение двухвальных шнековых смесителей, в которых оба рабочих органа одинаковы или различны как по конструкции, так и по режиму работы, дает положительный эффект. Чтобы повысить эффективность работы горизонтальных шнековых смесителей задают угол наклона лопаток или устанавливают по концам лопастей сплошную широкую ленту, которую чередуют с радиальными лопатками. Лопасти устанавливают так, чтобы две из них находились под углом 50° к оси вала (для продвижения продукта в направлении выгрузного окна), а третью размещают под углом 20° к оси в противоположном направлении (для создания встречных потоков продукта).
Вертикальные смесители применяются для приготовления комбикорма из сухих компонентов с различными добавками. Смесители данного типа представляют собой цилиндр с загрузочной воронкой и коническим днищем (опрокинутый конус), внутри которого располагают рабочий орган - вертикальный шнек. Точность смешивания у таких смесителей не очень высокая. Они особенно хорошо подходят для приготовления комбикормов в небольших хозяйствах, где нужны не большие объемы корма.
Принцип смешивания комбикорма вертикальным смесителем состоит в том, что в корпус смесителя загружают компоненты, которые занимают весь объем емкости. После включения шнека, частота вращения которого составляет 100... 150 мин" , нижние слои комбикорма поднимаются шнеком вверх и самотеком опускаются вниз вдоль стенок корпуса. Такой кругооборот в течение 5...8 мин способствует полному перемешиванию ингредиентов.
Производительность смесителей можно значительно увеличить если над ними устанавливать буферную емкость. Особенно это актуально для горизонтальных и диагональных смесителей. Пока идет процесс смешивания комбикорма в смесителе – загружается буферная емкость.
Как только смеситель опустошается – внизу накопительной емкости открывается задвижка и все ее содержимое в считанные секунды попадает в смеситель, где снова начинается очередной цикл смешивания.